|
System Description:
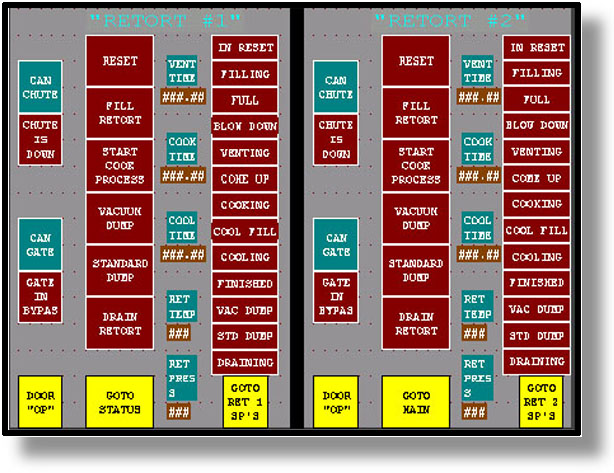
The heart of the system is a state of the art processor, with distributed
24 VDC, 4-20 mA analog inputs and outputs, and 24 VDC discrete inputs and
outputs. The control program uses standard ladder logic sequencing for simplicity
and ease of modification. Temperature and pressure are controlled using
PID (Proportional, Integral, Derivative) control loops within the software,
which interact with control valves to provide consistent, precise control.
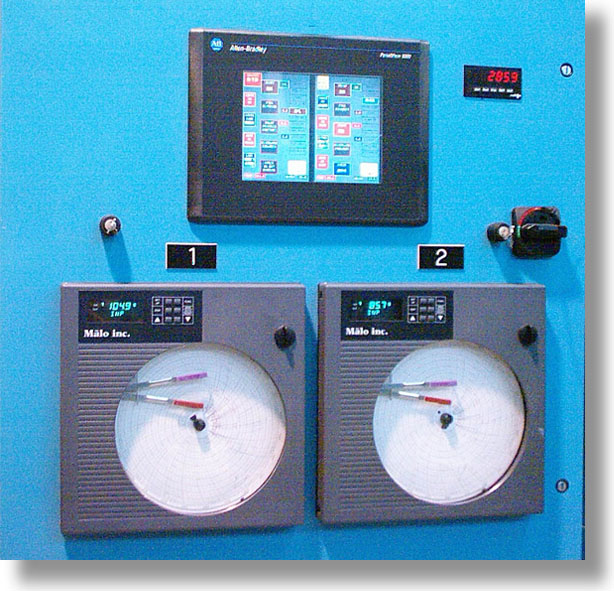
Operator interface is provided by color CRT Plant Floor Graphic Terminals,
which display the status of each individual retort. They also provide interface
with the processor for the purpose of set-point modification and status
update with menu driven software. This update can be developed either through
the touch screen or through communication with a personal computer.
This system offers the latest technology in control, quality assurance,
process flexibility, reliability, and security over conventional systems.
The use of state of the art, off the shelf industrial components, coupled
with more than 35 years crateless retort experience by Malo, provides the
best possible value to the customer in the area of computer controlled crateless
retort systems.
System Operation:
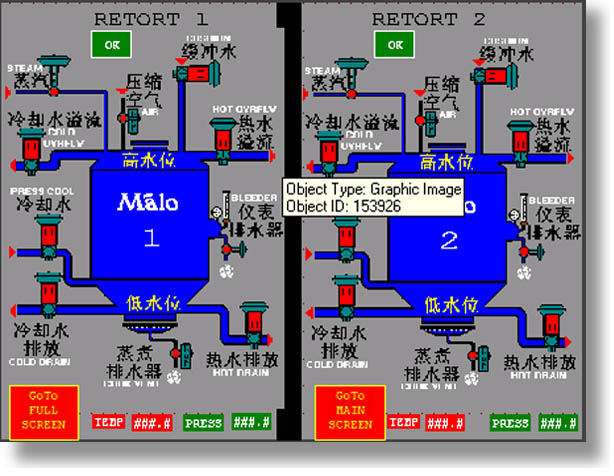
The system provides repeatable process control with
little or no adjustment between batches. Pre-operational setup and adjustments
are limited to inputting setpoints into the interface terminals. The set-points
are cook temperature, blowdown pressure, cooling pressure, time of vent,
time of cook, and time of pressure cool. The control system will retain
and hold these values until the product changes or the recipe changes, requiring
new values to be entered.
Safety Features:
The Malo Microprocessor based control system
incorporates safety features designed to prevent unprocessed containers
from passing through the retort due to operator error or misjudgment.
Once the top door has been closed and the START
button depressed, the bottom door cannot be opened until a complete process
cycle is accomplished. The top door can be opened again only after the system
has been RESET.
The system also provides an interlock to prevent
closing the top door with the can chute down. The system prevents the doors
from opening while there is pressure in the retorts. The system also automatically
controls the temperature and level in the reservoir tank and the level in
the canals.
Hardware Provided:
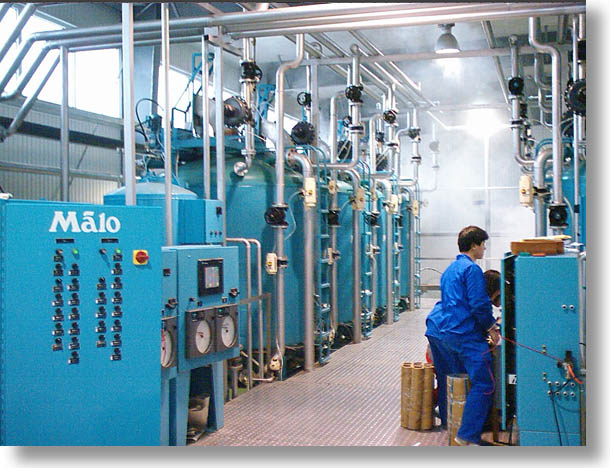
A. These items are in NEMA 12 enclosures.
|
1. Processor(s) - including appropriate discrete
input and output modules, analog input and output modules, network communication
modules and racks. The modules for each retort are located in the operator
panels which are located at each pair of retorts. The processor is located
in the first operator panel.
2. Touch Screen Color Terminal and Interface for
each two retorts.
3. Solid state, programmable 2-pen recorder for
each retort.
4. Power Supply and Power Distribution for instruments.
5. Can Counter(s)
6. Voltage Transformer for primary Operator Cabinet.
7. Operator Panel (A NEMA 12 enclosure) - Provides
top and bottom door controls, can diverter and chute controls, power switch,
start buttons, selector switches, indicator lights, solenoid valves and
I-P valve positioners, and high and low level relays. (There is one panel
for each two retorts.) IO modules for each pair of retorts are located in
the operator panels. |
B. Items provided for installation on retort.
|
1. Pressure Transmitter.
2. Temperature Transmitter. |
Software Provided:
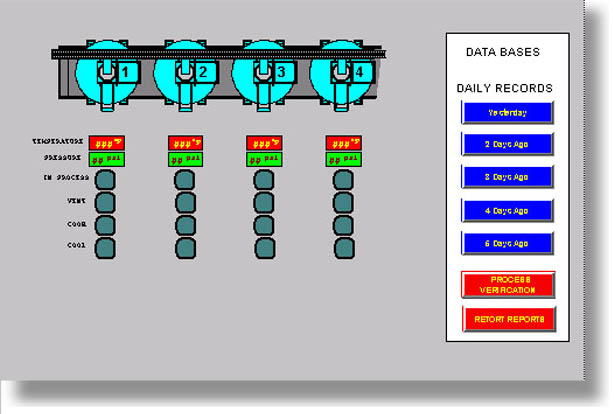
A. Developed by and proprietary to Malo, Inc., and is provided for customer
use on the quoted system.
B. Optional Software packages:
|
1. Data Acquisition: This program records the data of each process,
time stamps it and transmits it to a secure data base. The program inputs
include the process number, the process recipe, and can count. The program
prompts the operator to enter the FDA required temperature records and bleeder
status, and the electronic signature required by the CFR21. We provide shift,
daily, and monthly management reports with trending and alarms. The reports
can be reviewed from any network PC.
2. Recipe Download: This program allows for the storage of all recipe
set points and automatically enters the set points into the PLC. Recipes
will be listed on a recipe download screen accessible from any touch screen
panel. |
Return to top of page
Return to home page
|